
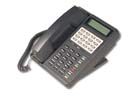
Help
- Contact Us
- Answers
- Site Map
- Promotions
- Policies

Sales and Customer Service
We believe in providing unmatched customer service and sales support for each product and service we offer. To this end, we will handle your account as follows.
Contact Information
You may reach us one of six ways.
ONLINE 24 hours a day.
PHONE between the hours of 8:30 am and 5:00 p.m. EST.
FAX 24 hours a day.
EMAIL 24 hours a day.
MAIL through rain or sleet or darkness of night.
OFFICE visit between the hours of 8:30 am and 5:00 p.m. EST.
Account Management
Your solutions will be provided by an outside Account Executive and an inside Customer Service Representative. Each is a phone call away when you are gathering information, requesting an estimate, seeking samples, placing an order, handling returns or discussing problems with your order.
Needs Assessment
Providing correct solutions begins with an assessment of your current needs, in-house capabilities and procurement process. Your Account Executive will use this review to identify the level and type of solutions that are most appropriate for you and your company. From this assessment, (s)he will propose solutions that provide you access to the latest technology and most efficient procurement methods.
Estimates
Getting estimates is a breeze! Your specifications are entered into a production management system that not only creates estimates, but handles work orders and invoicing. Once your pricing is computed, we can call, fax or email it to you. Remember, your estimate is based on the following.
Defined Specifications
We base all estimates on defined specifications. The more accurate the specifications, the more accurate your estimate. Any additional process required to finish your project that was not originally estimated (trimming, labeling, etc.) will be added to your invoice.
Availability of Dummies/Mockups for Difficult Projects
A dummy or mockup may be necessary to review before an estimate can be created. Most often, we can generate an estimate from customer-supplied specifications. Occasionally though, some specifications are so far beyond the realm of typical that we must see a dummy/mockup prior to estimating the job. This sample should be based on the exact sheet quantity, size and weight of all components (covers, book blocks, tabs and inserts) in the job.
Standard Turnaround
We base all estimates on standard production turnaround. Accelerated turnaround and overtime production requirements must be communicated with original job specifications, as all overtime required to meet RUSH deadlines will be invoiced.
Freight Terms of F.O.B. Our Dock
We offer freight terms of "F.O.B. Our Dock" unless otherwise stated. Be sure to add transportation costs to and from our facility, as these are not included in our estimates.
Acceptance
Your estimate is valid for up to 30 days from the printed date. Estimates older than 30 days should be confirmed.
Samples
Samples help bring printing project ideas to life. We can provide you with both "No Charge" and "For Fee" samples as detailed below.
No Charge Samples
Quite often, a customer will ask to see a sample of the finishing process being estimated. We welcome these requests and will provide samples that meet your customers needs as closely as possible. If we can fulfil these requests with inventoried supplies, you can order up to three (3) samples free of charge for the following services.
a) Wire Loop, Plastic Coil, Plastic Comb, VeloBind and Thermal Tape binding of documents requiring an 11" inventoried binding element
b) Manual saddle or side stitching
c) Screw post binding using an inventoried post
d) Guillotine cutting
e) Drilling using an in stock bit
f) Laminating using an inventoried film
g) Eyeleting using an inventoried brass eyelet
h) Manual fastening using an inventoried adhesive
i) Manual round cornering using an in stock cutter
j) Shrink wrapping using an in stock film
For Fee Samples
If "No Charge" samples do not meet your customer's needs, we can move to the next step - "For Fee" samples. The following circumstances will generate "For Fee" samples.
a) Samples requiring non-inventoried supplies that must be special ordered. All costs passed to us from the manufacturer or distributor to procure these supplies will be added to your final invoice or invoiced separately if the job never materializes.
b) Samples requiring any service not listed on the "No Charge" samples list. We will gladly process these samples for you, but will invoice you for each "For Fee" service provided.
Service Orders
Services are at the core of our finishing business. We have developed the following policies and practices to guide decisions involving service orders.
Advanced Notice
Advanced notice gives us a "head start" on your job. It allows us to make pre-production decisions, as well as place any special supplies orders. This is important for the reasons detailed below.
Jobs
Whenever possible, communicate when your job will arrive at our facility and when you would like to pick it up or have it shipped. This advanced notice helps us allocate equipment and labor resources proactively, rather than reactively. It also gives us an opportunity to order any additional inventory that may be necessary to produce your project.
Special Supplies Orders
Advanced notice becomes most important when special-order supplies will be used for your finishing project. Depending upon the item, manufacturing and shipping times may add from two days to two weeks to our production time.
Documentation
Each job you send to us should be accompanied by complete documentation. Be sure to cover the following with your paperwork.
Purchase Order
a) Record general order information such as the purchase order number, contact person, delivery address and due date.
b) List required quantity, acceptable overrun quantity, and special transportation needs and/or carriers.
c) List all operations necessary to correctly complete your job.
d) List special job details such as digital file names, element/mylar/foil colors, binding edge location, use of special covers, need for collating or binding edge reinforcing and number and diameter drilled holes.
Dummy/Proof/Blueline
a) Send a dummy/proof/blueline with each job to be finished.
b) Show pagination, binding edge location, foil/emboss location and finished trim size details, at a minimum.
c) Match the specifications detailed in the purchase order with the dummy/proof/blueline.
Order Confirmation
A simple, yet effective, way to ensure that your order is correctly understood is to request an order confirmation. We will review your new order against the respective estimate, update any new information and fax or email the confirmation to you. This document summarizes the products and/or services you are purchasing from us, as well as the completion date and shipping method required to meet your deadline.
Artwork
Correct artwork is the foundation of a correct project. Review the following artwork guidelines to ensure that your projects are destined for success.
Project Templates
You have access to a broad range of index tab and die press project templates on this site. Combine your artwork with one of these templates to create your own custom projects.
Custom Layout
If you do not have the time or capabilities, we provide custom typesetting and layout services for projects finished at our facility. We will not provide these services for projects finished by our competitors.
Customer-Supplied Artwork
You can supply your own project artwork twenty-four hours a day via the internet or during normal office hours by courier.
Proofs
If we are creating your artwork or you are unsure about the quality of your customer-supplied artwork, we can provide a proof for your approval. Communicate your need for the proof during the estimating process, as well as when the artwork process begins. If requested, the charge for the first proof is built into the estimate. Additional proofs will be billed to the order.
Dies
We have a broad inventory of house dies; however, we do not have a house die for every die line downloaded from this site. Flex Finishing will pay half the cost of a new die required to complete a project produced from a die line downloaded from this site. The die will remain the property of Flex Finishing and will be added to our inventory of available dies. You may also supply your own steel rule and brass/copper/magnesium die(s). These dies must not only be compatible with our equipment, they may also need to be modified to ensure the best results for your project. Once the project is completed, you may choose to inventory your die(s) at our facility for quicker turnaround of repeat orders.
Copyrights and Trademarks
Each body of work, whether it is a written document, photograph, painting, or logo, is covered by intellectual property rights. Unless you created the work or the rights have expired on the work, the use of the work must be approved or cleared by the owner of the work. Non-original copyright and trademark issues are the responsibility of party using the work. None the less, the printer bears additional responsibility to ensure that all copyright and trademark issues have been cleared. Our acceptance of artwork is under the sole condition that its use has been approved by the owner holding the intellectual property rights.
Press Proofs
Quality is in the eye of the beholder! As press proofs are not a normal part of the production process, we realize that sometimes they are needed. All requests for press proofs should be communicated with original estimate specifications. If not, press proofs must be handled with minimal disruption to the production process. Excessive proofing time, more than 15 minutes, will be billed at standard hourly rates for the respective equipment used.
Multiple Job Lots (Incoming)
We realize that the on-demand nature of some of your projects requires delivery of partial production runs. As we try to satisfy the needs of all of our customers, we also try to minimize processing partial production runs. We do this for two reasons. First, processing partial runs reduces our production efficiency by increasing equipment setup times. Secondly, it increases setup and processing waste, thus reducing your finished quantity. If your own production schedule prohibits delivery of a single lot, we will process your job in as few lots as possible to meet your deadlines. Remember though, each additional setup required to complete your job will be charged to your invoice.
Partial Production Processing (Incoming)
As end-user expectations for turnaround grow shorter and shorter, it often becomes necessary to make partial-quantity shipments of the finished project. We handle this in one of two ways.
Produced with One Setup
Your job is produced sequentially with the finished count accumulating until all pieces are done. You may need us to ship all currently completed pieces to meet your customer's deadline. We will gladly accommodate your request with any additional processing costs added to your invoice.
Produced with Multiple Setup
Occasionally, your customer will ask you to meet a nearly impossible deadline. If possible, we will re-schedule production of your first job lot to meet this deadline. The remaining job lots will be completed based on the original schedule with additional setup fees added to your invoice.
Additional Required Services
We realize that some end-users do not always supply you with all pertinent job specifications. This situation is most often resolved during the estimating process, as we attempt to pinpoint the exact services required to process the job. Quite often though, a job will enter production that requires additional services to properly complete. Additionally, jobs arrive that were not processed according to our directions or guidelines. The job may need additional trimming due to undisclosed bleeds or poor cutting quality on the part of the operator. Regardless, we stand ready to correctly prepare your material prior to moving to the next step in the finishing process.
Waste and Spoilage
The finished yield of your project is affected by waste and spoilage. Both terms are explained in detail below.
Waste
With any manufacturing process, your finished quantity never matches your input quantity. To ensure that we meet your required finished quantity, you must provide additional material for the setup and production processes. Depending on the complexity of the job and cost of the material, this "waste allowance" can be from one to ten percent. Regardless, be aware that setup and waste material will not be included with your completed job.
Spoilage
Spoilage on the other hand is not part of the manufacturing process. It is the result of poor printing, packaging or handling. If your material arrives with excess spoilage, an amount that will prohibit us from producing your requested quantity, we will email photographs of the damage to you. You may choose to have us start production of your job, but remember that any additional setup will be charged to your invoice.
Material Shortages
In the event that you do not supply enough material, we will contact you concerning the shortage. As long as you supply the balance of the material in a timeframe which does not jeopardize the completion of the next scheduled job, you will not incur additional waiting or setup charges.
Overruns and Underruns
Regardless of the technology, overruns and underruns are natural consequenses of the finishing process. Starting sheet counts, operator errors, equipment maintenance and environmental factors all contribute to yield the finished quantity. When indicating your desired finished quantity, you have the following four options.
Standard Trade Practice
You are invoiced for the actual quantity shipped, not to exceed a 10% overrun or 10% underrun.
No Overs
You are invoiced for the actual quantity shipped, which may exceed a 10% underrun.
Exact Quantity
You are invoiced for the actual quantity ordered, with any excess finished material being destroyed. Additionally, you will need to increase your estimate pricing by 10% to cover the additional processing required for this option.
No Unders
You are invoiced for the actual quantity shipped, which may exceed a 10% overrun.
Turnaround
Every customer has an expection for the timely completion of his(her) job. Some are reasonable and some are not. Our goal is to meet your deadlines during standard production hours; however, we do stand ready to meet your accelerated turnaround deadlines as well. To help aid in your understanding of rush processing, we have detailed each below.
Standard
We define standard turnaround as a production request that does NOT involve:
a) processing an unscheduled job the same day it is received
b) interrupting another customer's job that is currently running on or scheduled for a particular peice of equipment
c) using overtime or extended shift hours, including unplanned weekend work
Rush
Conversely, we define "Rush" turnaround as a production request that does require:
a) processing an unscheduled job the same day it is received
b) interrupting another customer's job that is currently running on or scheduled for a particular peice of equipment
c) using overtime or extended shift hours, including unplanned weekend work
Fees
"Rush" turnaround fees are computed as follows.
The greater of 15% of the Work Order Total or $60.00 for:
Perfect Binding
Automated Bookletmaking
Automated Collating
All Die Press Services
Automated Tab Cutting
Automated Mylar Tab Laminating
Automated Adhesive Fastening
The greater of 15% of the Work Order Total or $30.00 for:
All other job types not listed above
If a job involves multiple job types, individual Rush fees for each piece of equipment will be charged. Rembember, you can minimize "Rush" pricing, by discussing your quick turnaround and weekend work requirements during the estimating process as well as when you provide advanced notice for your job.
Cancellations
You may cancel service orders at any time during the process, but you will be billed for all services completed. Your special-order supplies orders may be cancelled, but you will be charged for any shipping and/or restocking fees applied by the distributor/manufacturer.
Minimum Service Orders
We have a minumum order subtotal for services of $25.00. Orders less than this will be billed at the $25.00 minimum.
Storage
You may chose to store the artwork and dies used to process your order at our facility. We will handle each as follows.
Digital Artwork Files/Film/Steel Rule Dies/Stamping Dies
We will store and backup your digital artwork files for a period up to 24 months from the shipping date of your order. We will also store your film, cutting dies and stamping dies up to 24 months from the shipping date of your order. Unless a repeat order is placed or a written request for return is received within this period, your digitial artwork files will be destroyed and your film/dies will be recycled without notice.
Production Supplies
We provide complimentary inventory management to customers requiring short-term storage of job supplies used in our production process. This material can be stored in our facility for a period not to exceed three (3) months.
Rights to Promote
Unless identified as "confidential" in writing at the time the order is placed, we reserve the right to use material that we have processed to
promote our quality and craftsmenship. The promotion may include, but is not limited to, use in brochures, sales sheets, catalogs, price lists, displays, web sites and samples programs.
Packaging
A project is not truly completed until it is delivered to and approved by the end user. The packaging policies and practices listed below will help you understand how we both can reach this goal.
Method
The two methods available for packaging your material are detailed below.
Corrugated Cartons
Corrugated cartons are best used when the end user needs a small handling unit. Cartons provide ample protection in an easy to handle package, unlike pallets. Material that will be stored and/or distributed in an office environment is best packaged in cartons. If cartons are used to package your project, non-discript, kraft-colored cartons will be used. You may specify the exact product count per carton or you may request "Carton Pack Convenient". The latter allows us to pack the best quantity per carton based upon the size and type of project.
Pallets
Pallets are the best option when the end user has a loading dock and will handle the material with a fork lift. Additionally, gaylords (corrugated wall and ceiling panels) can be used to add another level of protection for your material. Like corrugated cartoning, we will use non-descript packaging material to secure your material to the pallet.
Separator Sheets
As described earlier, material that is prone to transit damage should have some protective coating or covering. If the choice is made not to use this protection, paper or foam separator sheets may be used as follows.
Paper
Additional production time and cost may be minimized by using paper separator sheets. These sheets may be placed between each finished item or bound onto the front cover of a document for removal by the end user. They may be as inexpensive as 20# bond or as expensive as a super-smooth coated sheet. Regardless, using a sheet that can be processed as part of the job is the best option.
Foam
Foam separator sheets are very effective, but add both production time and cost to process the job.
Shipping and Receiving
A well packaged project serves no purpose until it is delivered. The policies and practices below will be used to handle transportation requirements of your project.
Freight Terms
Our freight terms are F.O.B. our dock.
Dock Hours
Our shipping and receiving department is open between the hours of 8:30 am and 5:00 pm EST.
Access
You have two access options when picking up or delivering material.
Truck Dock
Straight truck and LTL deliveries can be made to our standard height dock.
Van Dock
Van deliveries can be made to one of our ground level docks.
Methods
You have four transportation options as detailed below.
Customer Pick Up
Customers requiring instant, local access to our facility may personally deliver or pick up material during normal shipping and receiving hours. This is our default method of distribution for local customers.
Courier Company
Like customer pick up, courier companies can provide quick response to your local or regional transportation needs.
Common Carrier
We use UPS Ground for as our standard shipping method for next-day to seven day regional and national shipments of unpalletized orders that are distributed to one or multiple locations. Alternative carriers or methods are also available depending upon your requirements and deadline. We do not process orders for shipping on Saturday or Sunday, but can arrange for your order to be delivered on Saturday. If Saturday delivery is requested and the item is undeliverable, the additional carrier charges will not be refunded.
Trucking Company
We will use a trucking company for delivery of your material under the following circumstances:
a) Your order must be shipped on a pallet
b) LTL shipping is less expensive than common carrier shipping
c) There is one delivery destination
d) An above ground dock is available for loading/unloading
Drop Shipments
To minimize turnaround, we can drop ship your order directly to your customer's location. We can handle this one of two ways.
Regular Shipment
A regular shipment uses shipping labels that list our company address as the return address.
Blind Shipment
A blind shipment uses shipping labels that list your company address as the return address.
Split Shipments
We can split shipments to multiple locations, but there is a processing fee of $5.00 per address beginning with the second location. This processing fee is in addition to the carrier shipping charges.
Tracking
We use the most reliable and dependable couriers and carrriers in the business. Occasionally though, a package will need to be tracked to determine its whereabouts. We will gladly track any package that we have shipped for you.
Transit Damage
Transit damage is an unfortunate reality of modern transportation. Carefully review the following to gain an understand of how these issues are prevented and resolved.
Reason
Transit damage comes in the many forms. It may be contributory damage as a result of poor handling (ie. carton dropped from conveyor or carton punctured by forks on a lift truck) or non-contributory damage from normal and proper handling (ie. scratching of sheets by road vibration combined with press powders used in the printing process). Regardless, elimination of transit damage should be planned into the project right from the start.
Insurance
Common carriers and trucking companies usually provide a base level of insurance to cover losses from contributory transit damage. These levels are based on some combination of class, weight and/or value of the shipment. For instance, a trucking company may pay $6.40 per 100 pounds of the declared weight of the shipment. Loss over and above the base level will not be paid by the carrier. It is imperative for the print provider to consider this when planning transportation and to communicate any additional insurance needs prior to shipping. Flex Finishing will not provide additional transit insurance unless otherwise directed.
Responsibility
As the print provider, you are in the best position to understand the specifics of the paper and ink combination used and to make packaging and transportation decisions to minimize transit damage created by normal and proper handling. Special handling and packaging requests must be communicated with the original job specs so they can be incorporated into the estimate. If omitted, these special requests must be communicated prior to the actual production start of the job. Remember, it is the sole responsibility of the print provider to communicate special handling, packaging and insurance needs. In the event that damage does occur from normal, proper handling, Flex Finishing will help you process any claim but will not be held financially responsible for any loss.
Invoicing
Our focus on quality does not end with the finished project. It continues into the accounting process as well. We use the following policies and practices when handling invoicing.
Purchase Order Numbers
Purchase orders are a great accounting tool used to communicate and track job costs. If you use purchase orders and require the respective number be included on all job documents, please let us know. We can code our production management software to require the entry of your number prior to printing your work order. If a number is not required, the purchaser's name will be used instead.
Work Order Reconciliation
Upon placing your order, we convert your original estimate to a work order. The work order flows with your job through the production process. As services are provided, notes are recorded on the work order relative to the service. Additional services required to correctly process your job are also recorded. Once the production process is complete and you have received your project, we reconcile your work order as follows.
- Shipping quantities, including acceptable overruns, will be entered for each line item.
- Additional services required to correctly process your order will be added to the work order.
- Additional and/or updated supplies required to correctly process your order will be added to the work order.
- Supply manufacturers' price increases will be updated in work orders converted from estimates older than 30 days.
Price Variations
We make every effort to provide you with competitive and accurate pricing. Occasionally, we will need to adjust our pricing when a manufacturer's price increases or when a customer's order is different from the estimate. Changes in quantity, specifications and turnaround can all affect the final price of your order.
Tranportation Fees
Transportation fees can dramatically affect your final invoice price. We will handle them as follows.
Base Carrier Fees
Base carrier fees charged by the carrier are passed directly to your invoice without any markup. Your price is our price.
Special Handling
Additional fees charged by the carrier to process your shipment will be charged to your invoice. These may include, but are not limited to, fees for "Inside Delivery", "Notification", "Special Vehicles", "Waiting" and "Saturday Delivery".
Special Fees
Special fees also have in impact on your final invoice price. These will be handled as follows.
Small Order Fee
A small order fee passed to us by the manufacturer or distributor will be passed directly to your invoice.
Returned Check Fee
A $25.00 NSF fee will be charged for each returned check.
Taxes
Your purchases will be taxed based on North Carolina and Mecklenburg County guidelines unless:
1) You will be reselling the services or supplies, and
2) You provide us with a completed Resale Certificate.
Payments
Several invoice payment options are available for our customers. Policies and practices for each are detailed below.
Cash
Cash is an acceptable form of payment for orders picked up at our sales office. Due to the potential for loss, we do not accept cash payments through the mail.
Company Checks
New and existing customers may pay with company checks, however new companies must wait for check verification prior to leaving with any items. Additionally, all checks must be written from mature accounts. We do not accept starter checks.
Credit Cards
VISA, MasterCard and American Express cards are accepted via phone, fax and our website.
Credit Accounts
Payment terms will remain C.O.D. until a credit application has been processed and approved for your company. This takes approximately one week, but may take longer depending on credit reference response. Credit terms will differ depending upon the type of account listed below.
General Credit Accounts
General credit accounts are detailed on our Credit Terms page.
Trade Credit Accounts
Trade credit accounts are detailed on our Credit Terms page.
Refunds/Credits
A refund or credit for all or a portion of an invoice will be handled as follows.
Cash
Requests for credits or refunds made within 30 days from the original purchase date using "cash" will be issued back to the purchasing organization with a company check. Requests made after the 30-day period will receive a credit toward future purchases. Cash refunds are not available.
Company Checks
Requests for credits or refunds made within 30 days from the original purchase date using a "check" will be issued back to the purchasing organization with a company check. Requests made after the 30-day period will receive a credit toward future purchases.
Credit Cards
Requests for credits or refunds made within 30 days from the original purchase date charged to a "credit card" will be issued back to the repective credit card. Requests made after the 30-day period will receive a credit toward future purchases.
Credit Accounts
Credits due for purchases charged to a credit account will be issued back to the respective credit account.
Problems/Complaints
We want you to be completely satisfied and stand ready to assist you with production and supply issues. The following policies and practices will be used to handle problems and complaints.
Quality Assurance
Our primary goal is to provide you with only the highest quality solutions. We use state-of-the-art production technology, systemized quality control methods and highly skilled staff members to maximize the quality from your printed material. We stand behind our craftsmanship and guarantee to cure any defect in our work product or in the components we supply to process your job.
Quality Review Period
We have a consistent track record of providing high quality services; however, it is your responsibility to inspect these orders prior to delivery to the end user. To minimize complaints from issues beyond our control (ie. the end-users storage environment, handling practices and transportation methods), all quality claims must be reported within 30 days from your receipt of the material.
Quality Issues
Despite our best efforts, we will occassionally complete an order incorrectly. Reveiw the following to gain an understanding of how this situation will be handled.
Liability
With any manufacturing process, production errors will occur. If a job error occurs and we are unable to salvage your material. our liability is limited to "actual job costs". We will not cover "end-user markup" or "penalty fees". Additionally, we reserve the right to review job cost information upon request.
Remedy
Once job cost figures are determined and agreed upon, you will reimbursed one of two ways.
a) Dollar value trade-out for future services available based upon a period equal to the average daily age of your paid invoices
b) Dollar value charge-back to the associated invoice
Transit Damage
Transit damage is an unfortunate reality of modern transportation. Carefully review the following to gain an understand of how these issues are prevented and resolved.
Responsibility
As the print provider, you are in the best position to understand the specifics of the paper and ink combination used and to make packaging and transportation decisions to minimize transit damage created by normal and proper handling. Special handling and packaging requests must be
communicated with the original job specs so they can be incorporated into the estimate. If omitted, these special requests must be communicated prior to the actual production start of the job. Remember, it is the sole responsibility of the print provider to communicate special
handling, packaging and insurance needs. In the event that damage does occur from normal, proper handling, Flex Finishing will help you process any claim but will not be held financially responsible for any loss.
Initial Inspection
Upon arrival, we recommend that you open and inspect all cartons to ensure that your material has not been damaged in transit. If you find damage, mark the shipping documents "Received Damaged" and keep the shipping container, packing material and finished product for further inspection. You may be asked to photograph the damage and forward the photos to the transportation company.
Claims
Claims for loss, damage, shortages, delays or failures in shipment or delivery must be reported in writing to us within 10 days from the date of delivery to file a claim with the carrier.
Remedy
We will handle claims for damage to printed material differently depending upon the type of damage.
Apperance Damage
Appearance damage is defined as damage that degrades the apperance of the printed material, but does not render it unusable. This may include, but is not limited to, white spots on coated stocks (caused by a "sanding" effect of two sheets rubbing against each other during transit) or binding element depressions (caused by binding elements being pressed into adjacent documents by overstacking or dropping of the package). If requested, we will make a claim for financial reimbursement to the transporation company and will pass any reimbursement to you once the claim is settled. Reimbursement for this type of damage is occasionally granted.
Destruction Damage
Destruction damage is defined as damage that renders the printed material unusable. This may include, but is not limited to, torn/dogeared/missing document pages or crushed binding elements. We will make a claim for financial reimbursement to the transporation company and will pass any reimbursement to you once the claim is settled. Reimbursement for this type of damage is most often granted.
Confidentiality/Privacy/Security
Providing quality solutions is simply not enough. Trust is the other component of the partner relationship. We have employed the following policies to guarantee the confidentiality and security of your material and information.
Production Confidentiality
We understand the importance of confidentiality and pledge to handle your printed material as follows.
Projects
a) The material you identify as confidential will not be examined by vendors or other customers during the production process. This "confidentiality notification" should be communicated at the time the order is placed.
b) Your non-confidential, finished project may be viewed and/or released (as a sample of our work) to a third party outside our facility without your permission.
Employee Commitment
To further ensure the confidentiality of your printed material, we mandate that each Flex Finishing team member sign a confidentiality agreement as a condition of employment.
Security Guards
We welcome your use of security guards at our facility to secure highly confidential documents. Just communicate this requirement to your Account Executive and management will make all necessary arrangements.
Account Information Privacy and Security
You may provide both public and non-public personal information during a typical business transaction with Flex Finishing. We will guard and handle this information as follows.
Public Information
Public information including business contacts, addresses, telecommunication numbers, email address may be used for marketing purposes by Flex Finishing or a sister company.
Non-public Information
Non-public information including credit account and credit card information will be held in strict confidence. This information will not be used for any purpose other than to process your purchases.
Customer Account Information
All confidential customer account information is either stored on password-protected computers or locked in a high-security location.
Credit Card Information
The secure handling of online credit card information is a top priority. We employ a high-security internet transmission and storage technology known as SSL (Secure Sockets Layer) to process all credit card payments. During the checkout process you will enter your credit card information into a form originating from a secure server. SSL technology digitally encrypts this information and transfers it to our secure server for processing. A "closed lock" or "unbroken key" shown on your browser indicate that SSL technology is being used. Only credit card payments will invoke use of SSL technology. To further ensure the security of your credit card purchases, we:
- Do not save credit card numbers unless requested. Like shopping in a retail store, you will need to "hand" your card number to us for each online transaction. Since your number is not stored on our server, it cannot be viewed or stolen.
- Use equipment compatible with the V-code credit card confirmation process.
- Verify orders shipped to an address other than the credit card billing address. This helps reduce fraud by confirming the order with the credit card holder.
- Email an order confirmation that includes the items ordered, the shipping address and payment information (excluding specific credit card information).
- Accept printed final orders if you are not comfortable with online ordering. Simply print the order from your browser and fax or mail it to us.
- Use a leading security certificate authority to protect your online purchases. This provider offers a next-generation web trust service that combines state-of-the-art 128-bit SSL encryption and identity verification. The result is a new, unsurpassed level of security from your browser to our secure server.
Legal
We value and appreciate the time you spend on our site. Like our brick-and-mortar location, this site also has policies to help guide your usage.
Site Usage
This site is provided for the private use by current and prospective customers of Flex Finishing, Inc. Companies and organizations providing similar services are considered competitors and not welcome to use any part of this site.
Third-party Links
We welcome links to this site, but only through a written application process. Links should not be made to this site without the express written consent of Flex Finishing, Inc.
Copyright Statement
This site contains original content as well as specifications provided by our manufacturers. All information on this site is copyrighted and may not be used in part or in full without the express written consent of Flex Finishing, Inc.
File Download Terms and Conditions
The digital artwork accessed via this web site is the sole intellectual property of Flex Finishing. Flex Finishing provides these files for customers and prospects only. They are not provided for use by other print finishers. Flex Finishing grants you a 30-day license for the use of these die lines/templates. If the 30-day period expires without a respective job, the registered user will be invoiced this D.O. (Download Only) Fee. Without exception, you are not authorized to make this file available on any web site, or otherwise distribute, reproduce, copy or transmit in any form or by any means, electronic or mechanical, without the express written consent of Flex Finishing, Inc., Charlotte, North Carolina.