
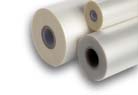
Laminating

Roll Laminating
Indicate the manufacturer and model of the digital printer when submitting specification for an estimate or an order. Because different printers require different film, review our film compatibility guidelines to determine the correct film for your project.
Offset printed sheets must be totally dry and void of excess spray powder prior to laminating. Wet ink will additional dry time, while excess spray powder may require a reprint of the entire job.
Synthetic ,vinyl and plastic stocks may blister when laminated. Be sure to communicate the use of these prior to estimating or processing your job.
Folded menus with a 1/8 edge seal should be designed with allowances for sealed edges.
Menus should be encapsulated with a 1/8 edge seal to protect against damage due to moisture.
For best results when folding laminated sheets, we will creased after laminating.
Matte films are available in a number of thicknesses and widths. These can exponentially increase the price of your project, though.
Provide additional stock for setup and testing.
Indicate the manufacturer and model of the digital printer when submitting specification for an estimate or an order. Because different printers require different film, review our film compatibility guidelines to determine the correct film for your project.
Offset printed sheets must be totally dry and void of excess spray powder prior to laminating. Wet ink will additional dry time, while excess spray powder may require a reprint of the entire job.
Synthetic, vinyl and plastic stocks may blister when laminated. Be sure to communicate the use of these prior to estimating or processing your job.
Folded menus with a 1/8 edge seal should be designed with allowances for sealed edges.
Menus should be encapsulated with a 1/8 edge seal to protect against damage due to moisture.
Matte films are available in a number of thicknesses and widths. These can exponentially increase the price of your project, though.
Provide additional stock for setup and testing.
Determine the outside diameter of the eyelet or grommet shaft prior to supplying pre-drilled stock
Provide additional stock for setup.
Keep sheets in a cool, dry environment. High humidity and direct sunlight can negatively affect the moisture content of the sheet. Too much or too little moisture in the sheet can create waves that become wrinkles in the finished product.
If possible, deliver sheets to us flat. Tubed or folded sheets (ie, maps) have a propensity to wrinkle.
Provide additional stock for setup.
Do not print rounded trim lines on the press sheets. Most often, these lines do not exactly match the radii of our cutters.
Provide additional stock for setup.
During the design process, make allowances for the location of the slot. This will help minimize punch-through of text or graphics.
Provide additional stock for setup.